Filtration and membrane separation processes
EnviCare® has consistently expanded its wealth of experience in the field of membrane separation technology since 1992. The implementation of numerous planning and related approval procedures, process validation and development on a laboratory and pilot scale, often with the involvement of leading technical universities, and finally, most importantly, implementation on an industrial scale, ensure today that the client is optimally advised.
Today, membranes are not only used in all areas of wastewater and process water treatment, they also represent a central unit operation in industrial production processes.
Likewise, hydrogen is increasingly and effectively produced in so-called PEM electrolysis plants, whose core – the stack – consists of the “proton exchange membrane” (or “polymer electrolyte membrane”).
Biomethane, in turn, is upgraded from raw biogas with the help of selective gas permeation membranes.
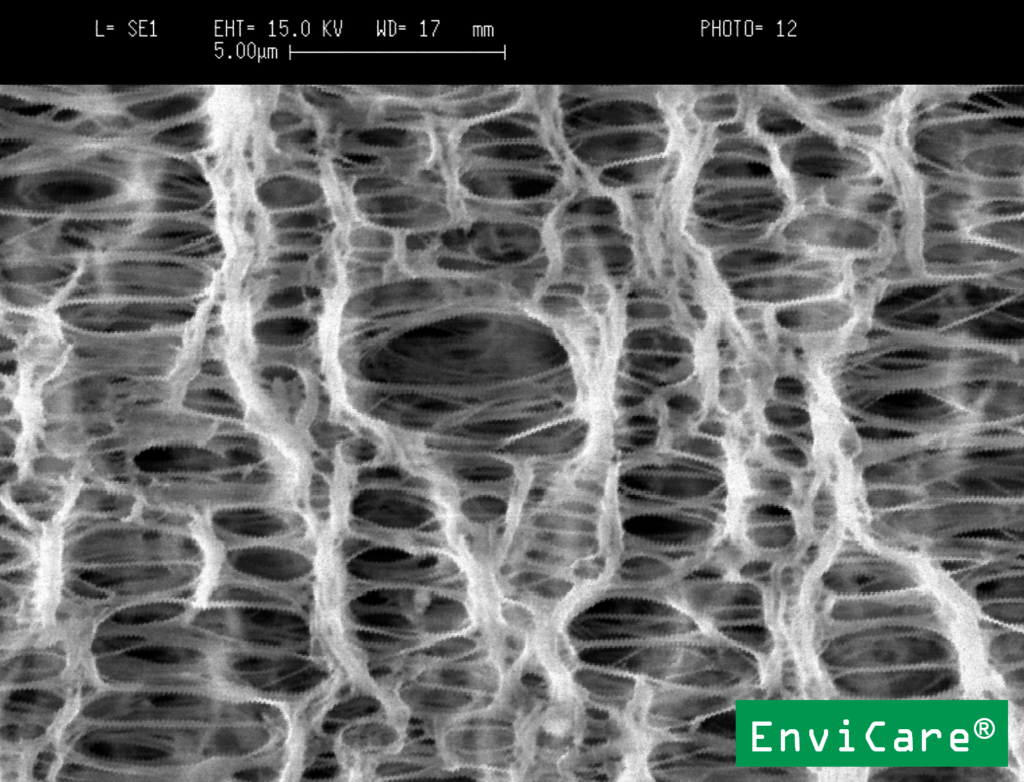
Membrane bioreactors
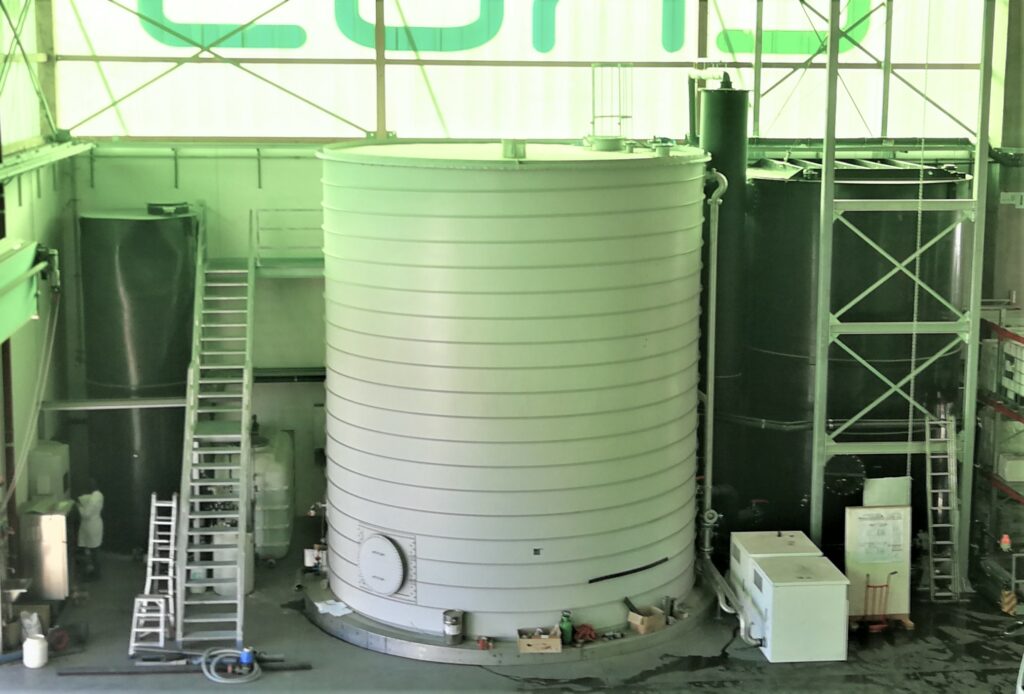
The conventional wastewater technology process is based on the principle of sedimentation of the activated sludge and requires the construction of large-volume clarification tanks in addition to complex machine technology (pumps, aeration, scraper).
Continuous progress in the development of new membrane materials today enables the use of membrane filtration technology in municipal and industrial wastewater treatment. Particularly in the case of expansion of existing plants or limited space, the higher purification capacity can be an important decision criterion for the use of membrane filtration plants due to the significantly lower space requirement (“footprint”).
Membrane-supported biomethane processing
An existing agricultural biogas plant currently produces renewable energy in the form of electricity (650 kW) and heat from renewable raw materials and agricultural products and residues in a CHP unit. In order to be able to continue the plant in the future, a membrane-based biomethane processing plant is now to be built with the aim of producing and feeding 460 Nm³/h of biomethane into the public natural gas grid.
The raw biogas contains 50 – 65 % methane, 30 – 48 % carbon dioxide and other trace gases such as hydrogen sulphide. After appropriate pre-treatment and subsequent membrane processing, the biomethane produced in this way is fed into the natural gas grid.
Gas separation membranes work on the principle of selective permeation through a membrane surface. The driving force for the gas to permeate through the membrane is the partial pressure difference of the gas between the retentate side (= inside of the hollow fibre) and the permeate side (= outside).
In the separation of carbon dioxide and methane relevant here, carbon dioxide permeates through the membrane with strong preference, while methane is retained.
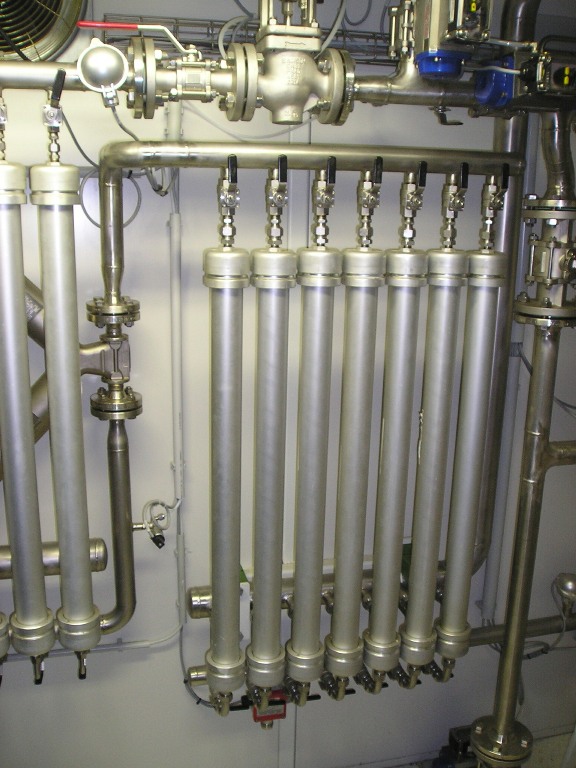
Hydrogen production with PEM electrolysis
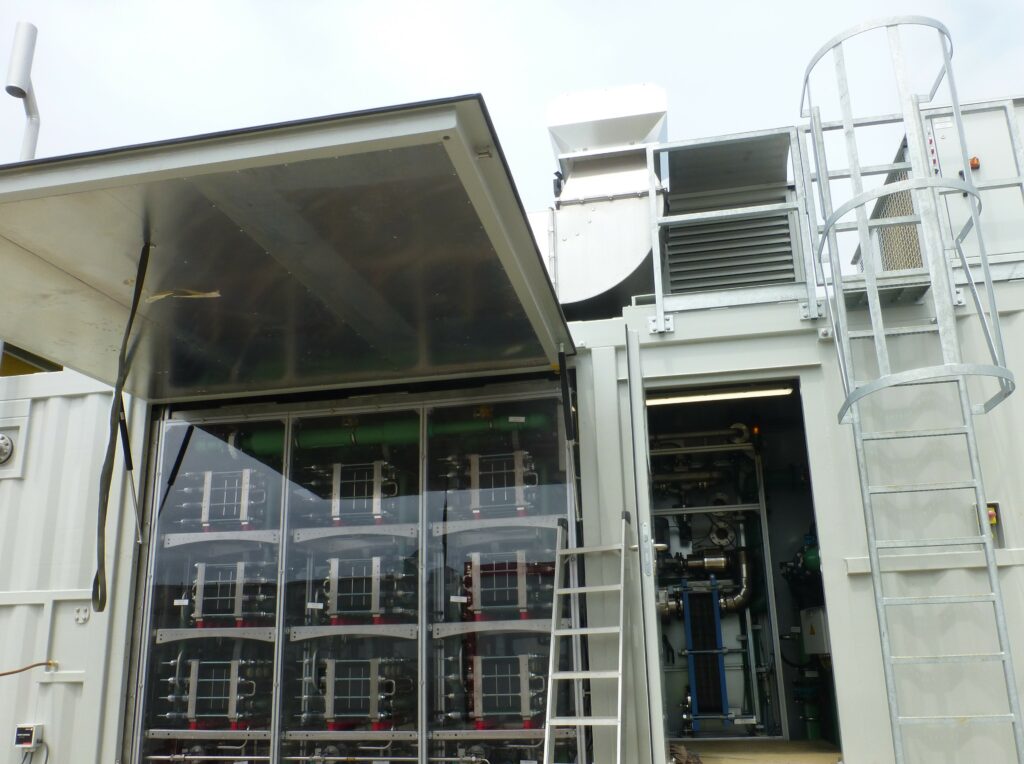
In an Austrian research project, green hydrogen and biomethane are produced as important core components in the process of converting the gas grid into a CO2-neutral structure. In the process, green hydrogen is produced on site through PEM electrolysis with energy from the photovoltaic modules. The larger portion of the green hydrogen is transported off-site for industrial use, while a smaller portion is used to upgrade the carbon dioxide (CO2) in the raw biogas of a regional agricultural biogas plant to biomethane through a catalytic methanation process.
Green hydrogen is produced by a 1 MW PEM electrolysis with a production capacity of 210 Nm³ H2/h. At the heart of the electrolysis are the stacks, which are connected to the ultrapure water circuit. Each stack consists of several cells, whereby each cell is constructed from two chambers (anode and cathode) separated by a proton exchange membrane (PEM).
The ultrapure water is pumped through the anode side whilst current is applied to the electrolysis stacks. Oxygen (O2), hydrogen protons (H+) and free electrons are produced at the positive pole (anode). The hydrogen protons migrate through the membrane to the negative pole (cathode) and gaseous hydrogen (H2) is formed with the free electrons. The gaseous oxygen (O2) remains on the anode side and is flushed out with the excess water from the electrolysis stack into the oxygen separator.
Microfiltration
With the microfiltration plant of a medium-sized dairy, the feasibility of splitting the wash water into 15v% high-fat and COD retentate and 85v% low COD filtrate was demonstrated on a large scale. The high-fat retentate is fed directly to the digestion tower via a hose line, while the low-fat filtrate is discharged via the gravity sewer as before.
On the one hand, this serves to avoid the bulking sludge problem in the aerobic purification stage of the sewage treatment plant, which has repeatedly occurred in the past, and on the other hand leads to greater gas production in the digestion tower.
On the one hand, this membrane-supported wastewater pre-treatment of the dairy solves the problem of bulking sludge in the wastewater treatment plant and, on the other hand, achieves a daily energy gain of approx. 2,400 kWh.
This energy gain is offset by the power requirement of the membrane filtration of 35 kW, resulting in a total net benefit of the installation of approx. 65 kW.
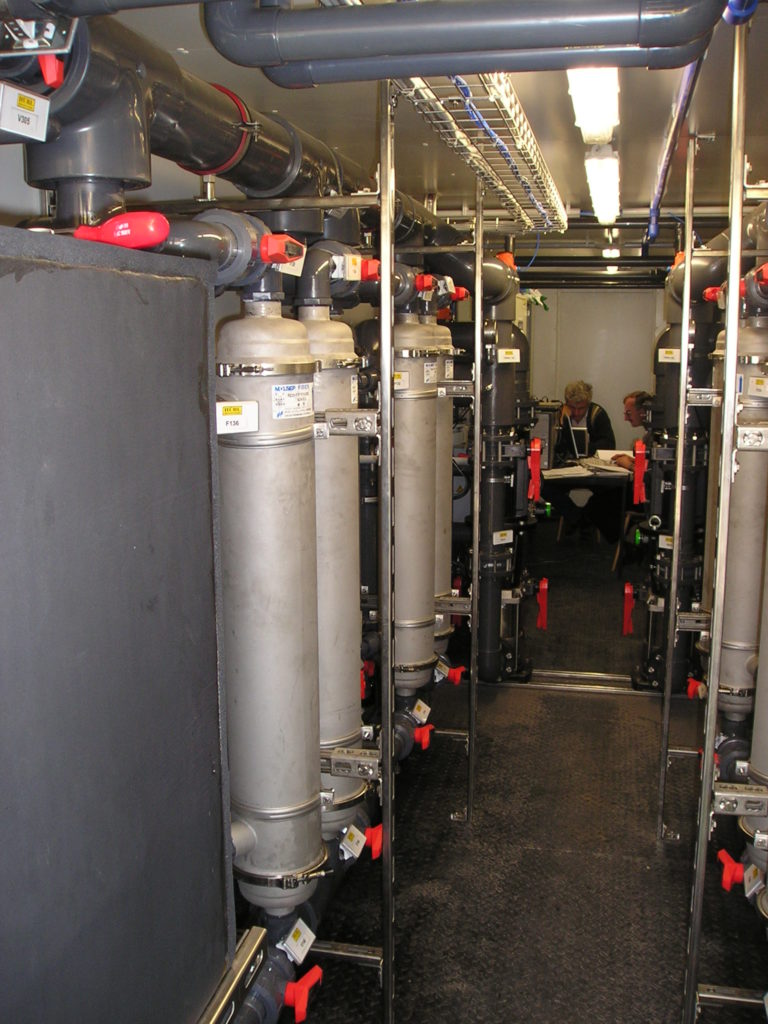
Nanofiltration and reverse osmosis
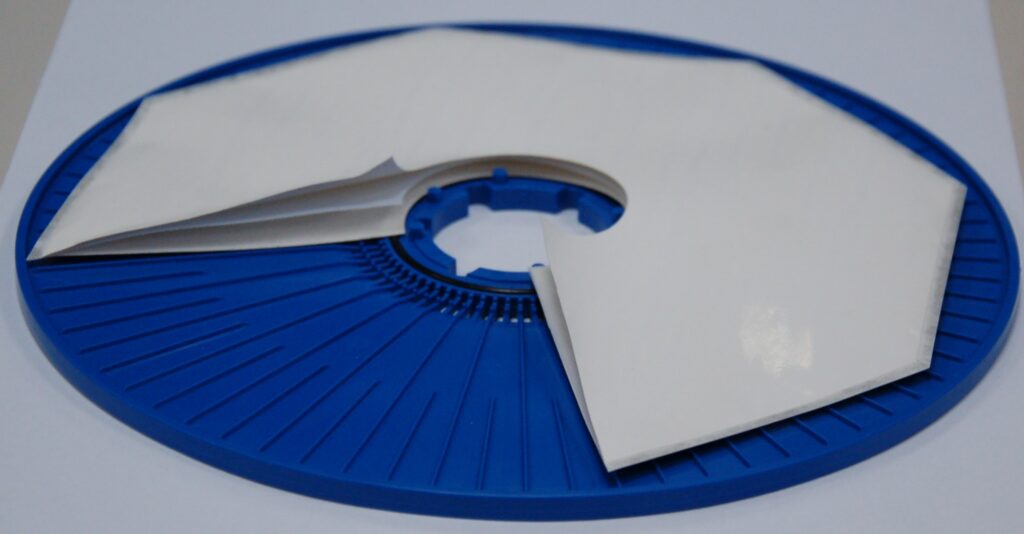
EnviCare® has decades of experience in the use of nanofiltration plants and reverse osmosis processes, especially in the field of process water treatment and landfill leachate treatment. The non-selective retention behaviour of reverse osmosis has great advantages here, as all larger substances are reliably removed from the pure water and, in addition, the quality can be monitored very simply and safely via reliable sum parameters.
The membrane acts as a real barrier here and reliably holds back bacteria, viruses and larger molecules according to the separation limit used. Alternative processes based on ozonation, UV irradiation, activated carbon adsorption, gravity separation or chemical treatment cannot guarantee this.
Membrane distillation
The development of mass transfer processes based on membrane distillation, which can be used e.g. for the direct extraction of nitrogen and phosphorus fertiliser from biogas slurry or from the turbid water of digestion towers, is also an exciting focal point of our R&D activity.
Membrane distillation (MD) is a thermal process in which only vaporous molecules diffuse through a porous, hydrophobic membrane. The liquid feed is in direct contact with one side of the membrane, but its hydrophobic properties prevent the liquid from penetrating the pores of the membrane due to the prevailing surface tension. The driving force of the MD is a vapour pressure difference between the warm feed side and the cold permeate side of the membrane.
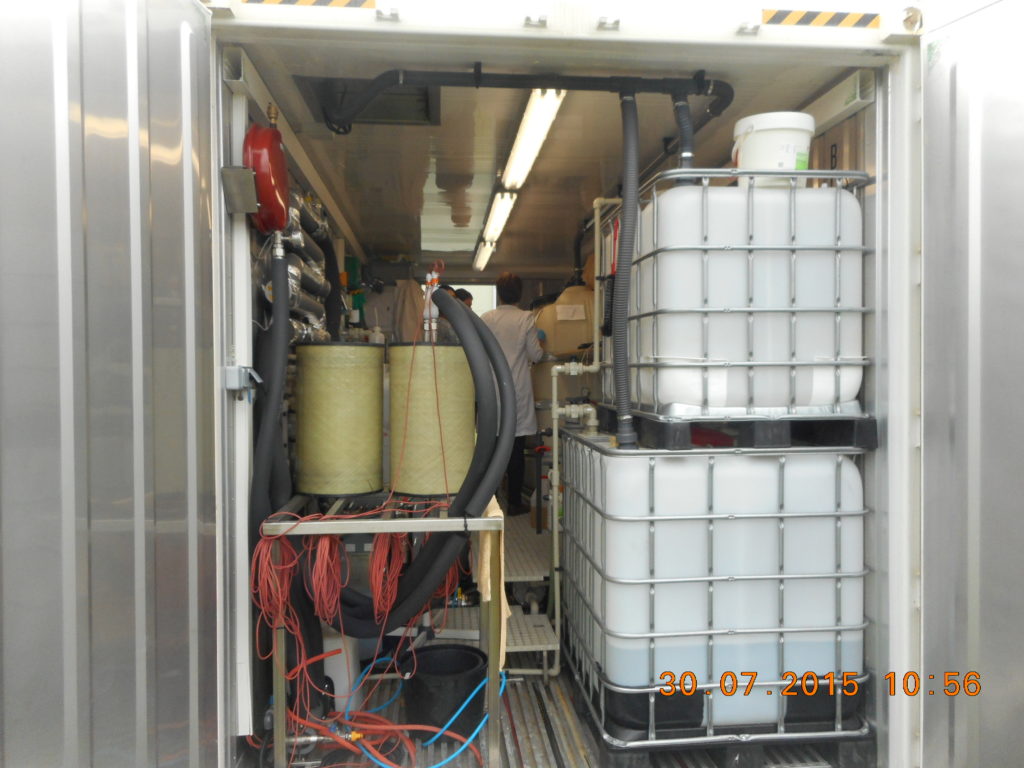
The thermal energy is required at comparatively low temperatures of 60 – 80°C and can be provided by waste heat from a combined heat and power plant or solar thermal energy.
Today, the MD is primarily used for the extraction of drinking water from seawater and brackish water and for the production of ultra-pure water from drinking water. The use of this comparatively “young” membrane process for the treatment of heavily polluted aqueous solutions is promising.
EnviCare® offers engineering services in the following areas:
- Membrane bioreactors
- Mass transfer – membrane distillation
- Micro and ultra filtration
- Nanofiltration
- Reverse osmosis
- Wasserstofferzeugung auf Basis von PEM
- Gas permeation – production of biomethane
We offer filtration and membrane separation process engineering for a wide range of industrial applications and always tailor our offerings to individual customer needs:
- Process engineering planning services
- Implementation and evaluation of pilot tests
- Handling tenders and official procedures
- Consulting (feasibility studies, concept development)